所有电子吊秤起重机在生产制造中,根据规范和客户要求,均规定额定的载荷重量,为了保护起重设备本身,在起重机规范中,每种起重机必须安装称重系统,能准确测量出所承载物体的重量,以确保起重机本身不受损坏。那么,安装重量称重系统就成为每种起重机必须的一套系统。
1.国内安装的称重系统一般构成
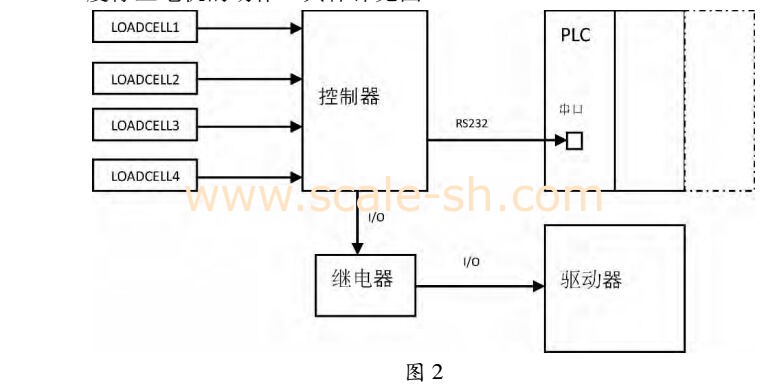
2.国内外称重系统工作原理对比分析
称重传感器通过采集器处理通过 RS485 送给控制器,同样地,RS485 信号经过电流变送器转换模拟量信号再传入起重机主控系统中( 一般为 PLC) ,信号经过了诸多硬件环节,而国内所生产重量传感器、采集器、电流变送器等硬件和市场诸多的其他电子产品一样,使用在起重机设备时,并未考虑到起重机的复杂工况,导致硬件不稳定或使用寿命短。故障率极高。而这种模式在国产产品实际应用中,几乎成了定式。
国外产品中,其动作原理和相关计算方法实际是类同的,实际操作中也能基本维持比较稳定的工作状态,但由于其控制器采购成本巨大,实际在应用中却难于推广应用。
但无论是国内和国外的产品,精兵简政才是最直接最有效的并且是故障率最低的一种方式,对于客户而言,准确的实施保护,稳定的运行,维护成本低是客户想要理想结果。随着可编程逻辑控制器的发展,其运算速度越来越快,对于复杂计算也能轻而易举的实现,起重机的称重控制器的工作能否由 PLC 完成呢,答案是肯定的。
3.以ABB为例,说明在如何直接在PLC中完成起重机的称重
原设计中,起重机重量传感器信号进入控制器进行处理,控制器输出的一路硬件为 RS232 进入 PLC 串口模块,PLC 直接接收重量信号; 控制器输出的另外一路为挂舱 I / O( snagload) 信号,该信号通过中间继电器的触点进入驱动器的 I / O 接口板,以最快的速度停止电机的动作。具体详见:
.jpg)
根据以上原理图,如果将上述功能转移到 PLC 中,则要同样实现 2 个功能,及在 PLC CPU 执行称重计算和 Snagload 信号的送出,除此以外,还要考虑一个运算速度的问题,特别是对于 Snag-load 的信号,当起重机发生挂舱时,需要第一时间进行保护,立即停止起重机的相关动作。下面我们就上述问题逐一分析并解决。
首先,在 PLC 内解决重量计算的问题,常规的重量传感器的控制器接收 4 - 20ma 的信号,根据理想线性变化的原理,在控制器内部实现运算,同时控制器还对干扰失真的部分信号进行相应的处理。
但对于直接进入 PLC 的模拟信号,通过 PLC AI 模块进行输入,PLC 读到的数据是原始的模拟量的数据。
根据重量传感器线性变化的特点( 理想) ,我们任意规定 2 个点,就可以确定斜率 K 和补偿值 B,实际上,由于称重系统的“0”点和额定载荷的“40”吨的两个点是做保护的两个关键点,松绳保护的重量一般在“0”点附近,超重是在额定载荷超过 10% 附近,同时额载的 80% 通常作为我们重量的预警。因此,我们通常选择这两个点作为称重系统的两个点。
根据 Y = KX + B 二元一次方程,称重时,能分别知道“0”T 和 “40”T 的 Y 和 X 值,这样,我们便能通过计算,分别计算出 K 和 B 值,也就确定了这条线性变化的直线。明白了其计算原理,通过编程,则可自动实现计算。
然而在实际应用中,通过基本原理计算的重量却往往出现报警,重量偏差较大,这又是怎么回事呢。原来,原设计中,LOAD-CELL 模拟量信号进入控制器,控制器首先消除干扰源,然后再进行计算处理。而 PLC AI 输入模块则是标准的产品,无法在硬件上改动以达到消除干扰的目的。通过分析,我们不难找到,模拟量的干扰源来自几个方面: 容性的静电感应、感性的电磁感应、和电源质量本身的射频或谐波的干扰等。我们可以通过提高开关电源的性能和使用类似双屏蔽的线路达到减低干扰源的目的。而事实上,吊机整体钢结构和使用 IGBT、可控硅等功率原件这些客观存在的固有干扰,其实是无法完全消除干扰源的,因此,需要在编程计算时使用更有技巧的计算。因此在编程时也需要加入“滤波”使来源数据更加符合实际状况,在此,引入一阶滞后滤波计算,即是在输出时将上次输出的值引入进行运算。这样虽带来了灵敏度减低,但却增加了稳定性,实质上也消除了尖峰值。
需要说明的是,snagload( 挂舱) 保护的运算是不得加装任何过滤装置的,因此在硬件上消除干扰必须要尽可能做到完善,现在一般吊机最基本的挂舱保护只有通过LOADCELL 的电子挂舱保护,虽然现在很多挂舱增加了液压油缸挂舱保护,但最第一时间反映挂舱情况的则是电子挂舱,挂舱保护在设计时须尽量减少运算的环节,最好是将重量转成相应的输入原始值进行对比,当挂舱动作,PLC 直接输出进入驱动器,紧急停止驱动器,以最短的路径和时间来实现设备动作的停止。
有了前端消除干扰,数据输入的稳定性增加了,根据 Y = KX + B 的方式编程如下:
GeneralInterlockReady-外部条件Ton2(In:= GeneralInterlockReady,
PT:= WaitingTime,
Q =>GeneralInterlockOk)
(* Load cell value stored in a variable *)LoadCellLeft1Act:= LoadCellLeft1ActValue.Value;LoadCellLeft2Act:= LoadCellLeft2ActValue.Value;LoadCellRight1Act:= LoadCellRight1ActValue. Value;
if CalibrationChecked then
LoadCellLeft1ActOut.Value:= LoadCellLeft1Act * Load-CellLeft1LoadScale + LoadCellLeft1TareOffset;
LoadCellLeft2ActOut.Value:= LoadCellLeft2Act * Load-CellLeft2LoadScale + LoadCellLeft2TareOffset;
LoadCellRight1ActOut.Value:= LoadCellRight1Act* LoadCell-Right1LoadScale + LoadCellRight1TareOffset;
LoadCellRight2ActOut.Value:= LoadCellRight2Act* LoadCell-Right2LoadScale + LoadCellRight2TareOffset;
.jpg)
常规的程序是需要手动计算的,当使用上述程序,则只要称重一次,则可将 K 和 B 值保留,并一直沿用,直至原始数据出现漂移,则需要在此核准重量,重新计算对应的K / B 值。
消除了数值瞬时异动问题,LOADCELL 称重是不是就稳定了呢,在实际应用中,由于吊机工作特性,重量的漂移还受到加减速或是启动和停止的瞬间。这是由于吊载物在启动和停止瞬间加减速度是最大的,根据F = ma,钢丝绳(即loadcell) 需要承载的重量除了吊载物外,还需要加上ma的重量,在实际操作中,启动和停止的瞬间的最大差值可能达到10T 左右,虽然loadcell 反映了实际承受的重力,但却无法客观反映实际吊载的重力,因此,仍需要消除在加减速过程中带来的重量变化。吊机在操作过程中各种工况并不是有规律性的,吊载重量可能每次不同,人为给定的速度也可能每次不同。也就无法规定一个匀加速或匀减速作为一个定值“a”作为计算的依据,并且,如果通过计算每个时刻的“a”值来计算增加的承载力,是一个精密和复杂的计算,也不适合用于 PLC 编程。在调试过程中,通过拍摄波形图,我们不难发现,重力增加最大的时候发生在吊载物在启动和停止的瞬间,这个时刻也恰巧是加减速最大的时候,也是速度给定和速度反馈偏差最大的时候,一般在驱动器调试中,给定和反馈的偏差值不大于 3% ,是属于正常偏差范围,而正常作平滑运动时,均不会超过 1% ,超过 1% 的正常工况则大部分属于在加减速时刻。因而,当给定和反馈值大于 1% 时,可以给出一定的重量补偿值。那么这个补偿值又该如何确定呢,假定上下运动物体的最大运动速度为 2. 5 米 / 秒,加减速时间为4S,根据 Vt - V0 = at,再根据 F = ma,不难算出在最大加减速时,理论上可产生增加的 F 为是当时载重量的 62. 5% ,通过动滑轮的转换,仍可达到 31. 25% ,因此,假定额定负载为 40T,最大设定补偿值可以为 40* 31. 5% = 12. 6T,因此在加减速期间,可以将其最大值设定为 52. 6T,这样就避免了在启动和停止瞬间的超重值了( 程序量比较多,在此不作详解) 。
4.总结
我们可以根据计算出来的重量值,分别设定,单角、单边、挂舱和总重量的报警设定值,同时,设定在着箱时的松绳值。单角和单边需要根据设备设计时的安全系数来确定,而且也要考虑钢丝绳的承载力,总重量的超重报警一般设定为 110% 。由此,吊机中的重量称重和保护系统就全部完成了。